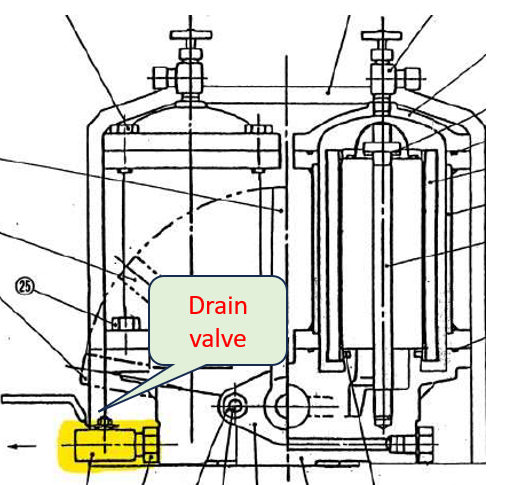
Case study: Pressurised oil spray causing fire at auxiliary engine (AE)
What happened?
While preparing for AE3’s routine filter cleaning, Low Sulphur Marine Gas Oil (LSMGO) that was under pressure in the residual line, sprayed from the duplex fuel filter cover onto the exhaust gas branch pipe of AE2, which was running at the material time. The spraying of the LSMGO onto hot surfaces of AE2 resulted in an instantaneous fire. There was no reported injury. See Screengrab 1.
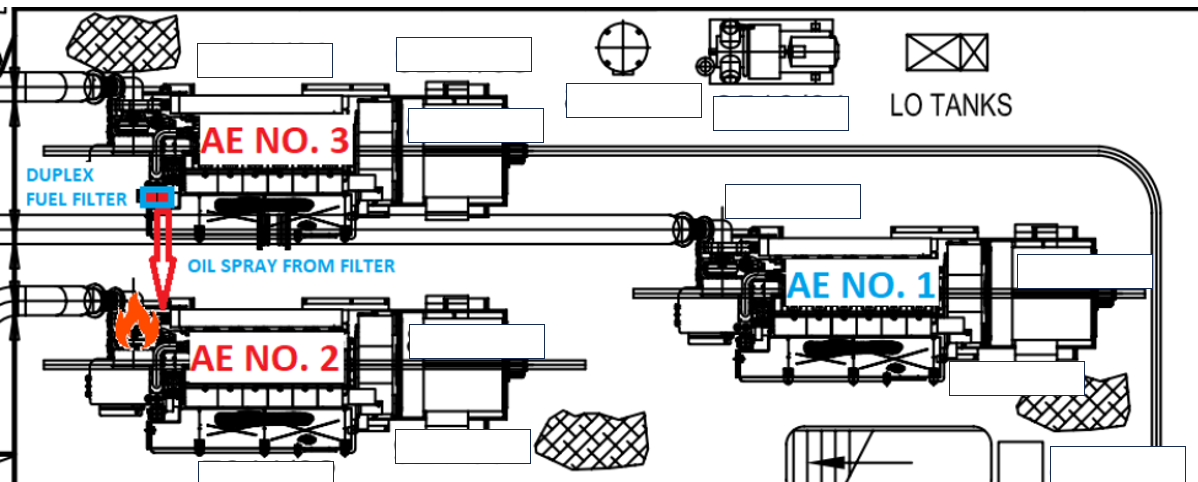
Why did it happen?
When the engineer wanted to vent the residual pressure in the line from the vent valve, he noted the latter was frozen. He therefore resorted to release the said pressure by loosening the duplex fuel filter cover bolts. When the cover was loosened, oil sprayed out onto AE2’s exhaust branch pipe.
The company had identified the following three root causes:
1.Inadequate valve isolation. While the main fuel in/out valves were isolated by the engineer, he had omitted to isolate the duplex fuel filter valve.
2. Incorrect venting procedure. The correct venting procedure is through the vent valve, which froze at the material time. However, an alternate method was available, i.e., open the dedicated drain valve, which can be operated separately and to partially drain the oil and relieved any residual pressure. Thereafter, the cover was to be carefully crack-open to check if pressure still exists, before opening it fully. See Screengrab 2.
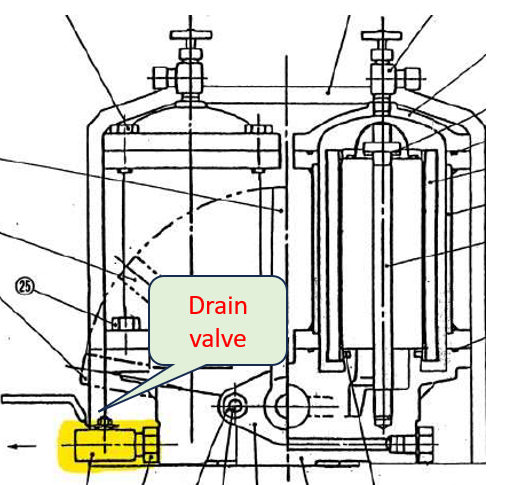
3. Inadequate protection on high temperature surfaces at AE2. AE2 turbocharger high temperature surfaces were not adequately insulated. This permitted the sprayed oil to come in contact and caught fire.
Case study: Pressurised oil spray causing injury
What happened?
While making rounds, senior engineer (SE) found fine fuel oil (FO) spraying around AE No. 4 (AE4) FO filter. SE told junior engineer (JE) to investigate the said spray. JE isolated AE4 by shutting the starting air and FO inlet/outlet valves. JE then opened the FO filter cover and found its O ring damaged. JE cleaned the filter and boxed up the cover with new O ring. After completing the job, JE opened the above FO inlet/outlet valves. After confirming no more leak from the said filter, JE went to start AE4 from the engine control room (ECR). He went and check on AE4 and found no leak. He started to square up around AE4’s area. Suddenly, the said filter started to splash out FO. JE asked another junior engineer (AJE) who was in the vicinity to start another AE from the ECR. Meanwhile, JE attempted to shut FO inlet valve that was near the FO filter. JE’s attempt had resulted in FO burns on his right hand and tainting of his boiler suit.
Why did it happen?
One of the bolts from the FO filter cover was found to have its threads damaged. This caused the filter cover not being boxed back with adequate tightness, hence the hot and pressurised FO spraying out from the cover. See Screengrab 3.
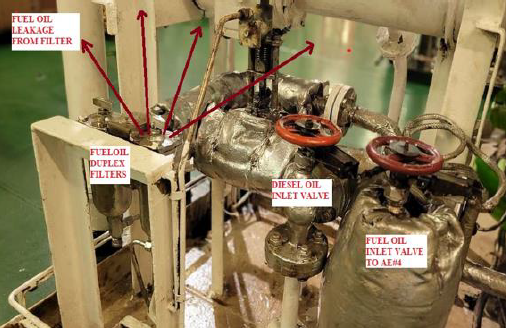
Additionally, the company had identified the following three root causes:
1. Failure to ensure all bolts for the filter cover were in good conditions.
2. Incorrect method to stop the FO spray. Essentially, the correct method to stop the FO spray would be to use remote closing valve, instead of the above FO inlet valve. See Screengrab 4 below.
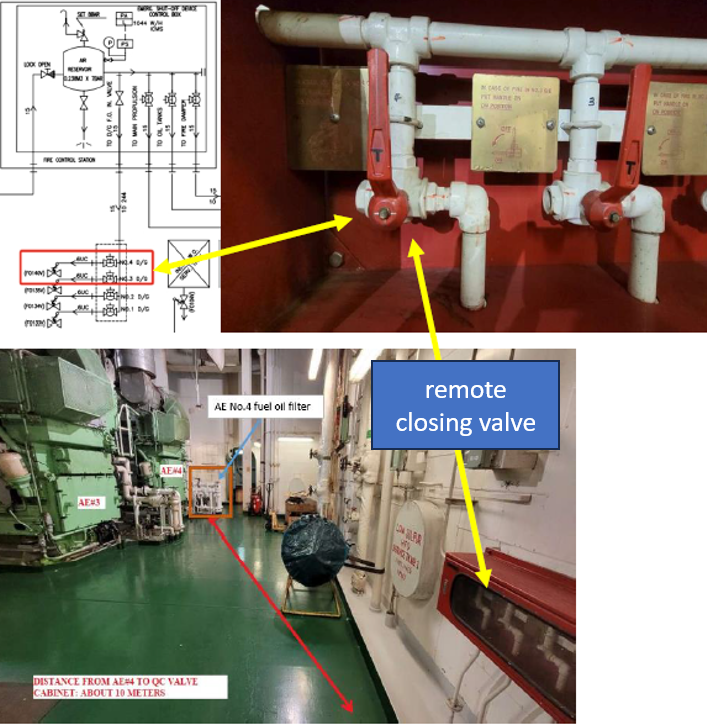
3. JE was not situationally aware of the spraying hot and pressurised oil which could cause burn injury.
Conclusion
The above two incidents happened from the same source, but caused different damage, i.e., fire and personal injury. Ship owners and managers are urged to consider the above root causes, and to discuss them in the appropriate platform. Additionally, it would be beneficial to learn from these incidents to strengthen the company’s safety management system (SMS).