Insight on Pilot Ladder Safety
In two recent and separate near-miss incidents in Singapore waters, the respective pilots suffered injuries as the pilot ladder in use at the material time parted during the disembarkation.
Incident 1
While the pilot was disembarking from the vessel, the forward side rope of the ladder parted about half-way down the (starboard) pilot ladder. The pilot suffered minor injuries (less than 72h medical leave) when he jumped onto the launch from a height of about 1.5m. The weather was fine with good visibility and minimum sea. This incident highlights the importance of continuous vigilance on the condition of personnel carrying equipment such as pilot ladders.
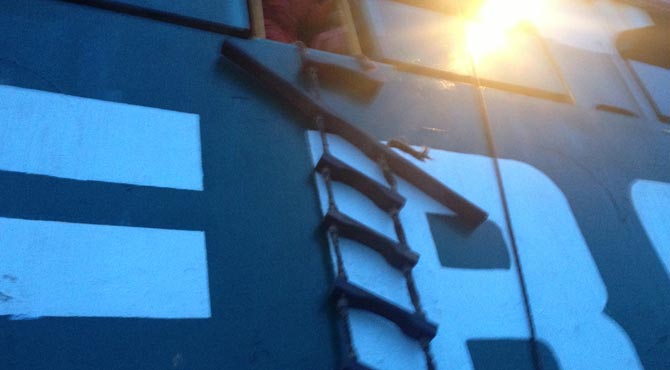
The broken part (weak link) was along the section of the side rope that passed through the hole on the wooden step (25mm depth).
Incident 2
As the pilot disembarking from the ship stepped on the deck of the pilot launch, he noted that the starboard pilot ladder was parting in the middle (both side ropes). The pilot sustained minor outpatient injuries due to the failing ladder. The weather was fine with good visibility and minimum sea.
According to the owners, both side ropes were renewed by the crew less than a year prior. In addition, as required under the company’s Safety Management System, the pilot ladder was last inspected and found fit by the crew a month before.
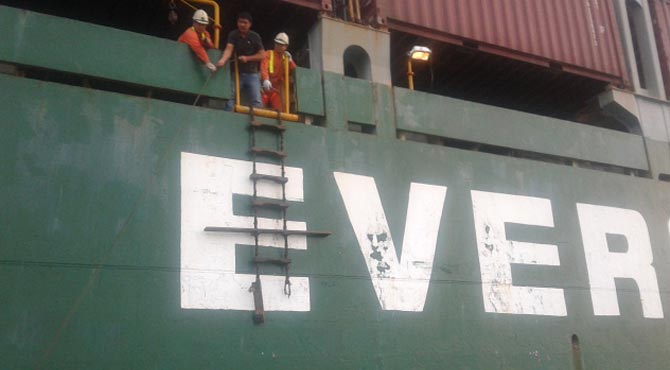
Starboard pilot ladder parted in the middle (on both sides of the rope)
MPA’s investigations revealed that the breaking stress of the side ropes used in the ladder were not in compliance with IMO Resolution A.1045(27) “Pilot Transfer Arrangements”. Ropes with lower breaking strength (i.e. 17 Kilo Newtons vis-a-vis the required 24 Kilo Newtons) were unintentionally supplied to the ship, and the crew had assumed all was well and used the ropes accordingly.
Following the incidents, the respective owners replaced pilot ladders onboard while issuing fleet-wide advisories to check for compliance with IMO Resolution A.1045(27) “Pilot Transfer Arrangements”.
We would like to remind shipowners and managers to ensure that Master, officers and crew onboard Singapore ships are aware of the risks associated with allowing embarkation or disembarkation of personnel using unsuitable and non-compliant pilot ladders. The ladders should be regularly inspected and physically tested by a responsible officer onboard prior to being allowed to be used for embarkation or disembarkation.
Lessons learnt – Flash fire onboard coastal tanker
In a recent incident, in fine weather and light wind conditions, a fire was reported onboard a foreign registered coastal tanker (LoA 48.0m, GT 297, built 1986), which was anchored at the Eastern Petroleum ‘B’ Anchorage. The tanker had on board about 130 metric tons of heavy fuel oil (HFO) cargo. There was no pollution from the incident but the tanker sustained substantial damages to the pump room and required extensive repairs.
As a result of the incident, 3 crew members suffered burn injuries and were sent ashore for medical treatment. One of the crew members later succumbed to his injuries while the other two recovered and were subsequently discharged from the hospital.
According to witness accounts, the flash fire occurred when a crew member was trying to switch on the electric driven pump in the vicinity of the pump room entrance. It was noted that the pump room ventilation fan has not been working for some time and crew were using an electrical portable fan to ventilate the pump room. It was also noted that the pump room bilges were not kept clean and leakages of cargo from leaking pipes and valves had accumulated in the bilges.
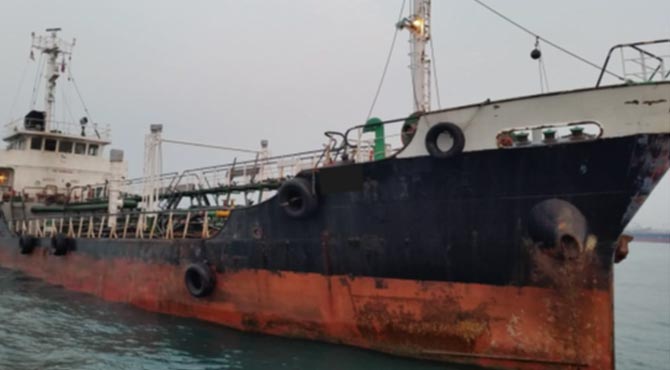
Image of the ship which was involved in the flash fire incident
MPA’s investigations revealed that the flash fire in the pump room was most probably due to ignition of a cloud of flammable mixture of hydrocarbon gasses in the pump room, caused by sparks or heat which could possibly originate from the defective electrical equipment or electrical fixtures in use.
Other contributory factors include:
Failure of the crew to monitor pump room atmosphere for presence of flammable gas, apparently due to false sense of security as the ship was loaded with HFO – a high flashpoint cargo;
Poor maintenance of pipe-lines, valves and ventilators inside pump room;
Poor maintenance of electrical equipment onboard, including use of non-approved equipment;
Poor housekeeping inside the pump room (i.e. bilges were not cleaned to remove leaked cargo (HFO) and sludge);
High ambient temperature
Ship’s crew are reminded that high flashpoint cargo such as HFO can pose hazards in high ambient temperatures which may cause the lighter factions in the fuel oil to evaporate. Lack of appropriate ventilation in the space may also cause pockets of flammable gasses to form, which can be ignited by a spark or other sources of ignition. It is therefore important that only approved equipment are provided onboard and regular checks are made to detect the presence of flammable gases.